Foresters and loggers utilize many different pieces of equipment in order to cut and process trees. In this post we will discuss some of the basic types of equipment most commonly used in forestry and logging applications.
Feller Bunchers
Feller bunchers are used in both thinnings and clearcuts to grab, cut, and stack trees in a quick, controlled manner. Feller-bunchers self-propelled machines with a cutting head capable of holding more than one stem (trunk) at a time. There are both wheeled and track-driven feller-bunchers with different capabilities: tracked machines are slower than wheeled, but are also more stable on steep surfaces. Some feller-bunchers have self-leveling cabs, allowing the operator to remain oriented correctly even when on grades up to 50%. Tracked machines are also capable of operating on wet and loose surfaces where wheeled machines are not able.
Wheeled feller-bunchers drive directly up to each tree in order to fell them, as the cutting head is mounted directly to the machine. Tracked feller-bunchers make use of an articulating boom with the cutting head mounted on the end, allowing them to clear out a 360° area around the machine before moving to a new area. This is also useful in stacking trees as they are cut down, operating much more efficiently than wheeled machines.
There are three types of cutting heads: felling heads, bunching heads, and processing heads. Felling heads are used to cut single stems with no additional processing capabilities. Bunching heads can carry multiple stems, but also have no processing ability. Processing heads are capable of both cutting and processing trees in a short time.
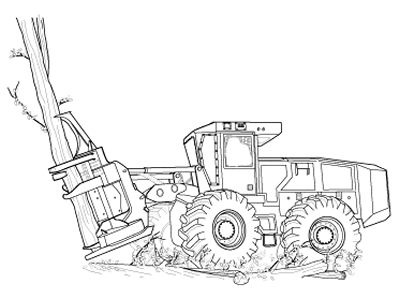
Drive to tree feller-buncher
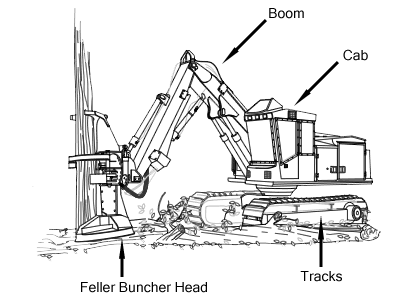
Swing boom feller-buncher
Delimbers
Delimbers are essential in forestry and logging work. Delimbers are used to remove the limbs from felled trees, making them easier to handle and transport off of the jobsite.
There are three basic methods for delimbing a tree: gate, flail, and pull-through. All three are landing-based, relatively low-cost, and most suitable in applications where the quality of the remaining wood is not a concern.
Gate Delimbers
Gate delimbers consist of steel tubing welded into a grid pattern. Gate delimbers may have an integrated support structure, or consist of a simple flat grid that is tied to standing trees. A grapple skidder moves a load of trees through the gates, thereby breaking off the limbs from the trunk as it is pushed through the grid. Gate delimbers are used in conjunction with a chipper or as part of a system that loads the delimbed stems directly onto a truck.
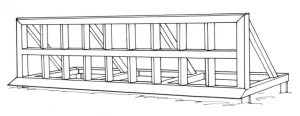
Gate Delimber
Pull-Through Delimbers
Pull-through delimbers are horizontal processors which lack a feeding mechanism or measuring capabilities. Pull-through delimbers are either standalone unites or mounted onto a trailer, often the same trailer as the loader for stability. The loader picks up felled trees and places them in the pull-through delimber, where a system of knives (typically three) grip the base of the trunk in order to pull the tree through the processor. Many models also feature a topping saw to remove the head of the tree. Pull-through delimbers provide a cleaner stem than gate delimbing and usually don’t require any additional processing prior to truck loading.
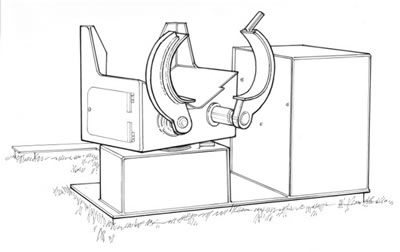
Pull-through delimber
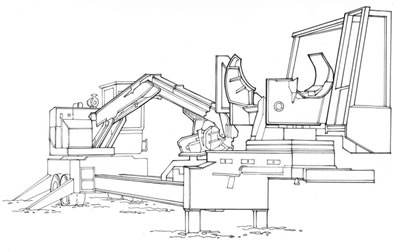
Pull-through delimber and loader mounted on trailer
Flail Delimbers
Flail delimbers consist of rotating drums with chains mounted to them. Flail delimbers are useful for dealing with smaller trees from dense stands with small limbs. The chains break off the limbs as trees are fed through the drum. Flails may be either self-feeding or require a loader or skidder to pull trees through. While the chains break and remove limbs, they also remove the bark from the tree. This can be useful when trying to achieve ‘clean’ chips (chips typically containing <1% bark content), which are used for making pulp and paper.
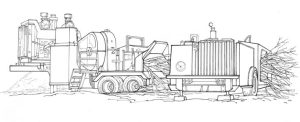
Delimber (right) feeding into a chipper
Log Loaders
Log loaders are used for sorting, moving, and stacking cut logs. There are wheeled, tracked, and truck-mounted log loaders. Hydraulically operated grapples are used to grab and control logs as they are moved into piles or onto trucks.
There are a few different types of log loaders. Knuckleboom loaders have articulating booms with fast hydraulic systems, allowing them to quickly raise, lower, and rotate in order to accurately place logs. Knucklebooms can be wheeled, tracked, or truck-mounted. Wheeled loaders can also use a set of forks with a grapple n order to pick up and load large numbers of logs at once. Trailer-mounted loaders are boom type loaders attached directly to the log truck. Truck-mounted loaders are used for loading shortwood and decrease the payload that the attached truck can carry.
There are also different types of grapples can be used depending on material, log size, and number of logs carried at one time.
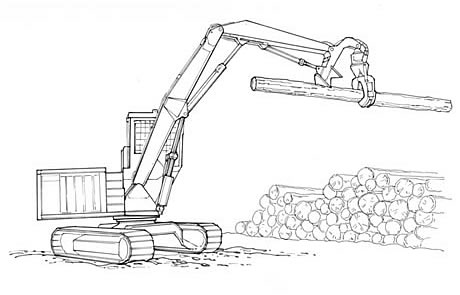
Log loader
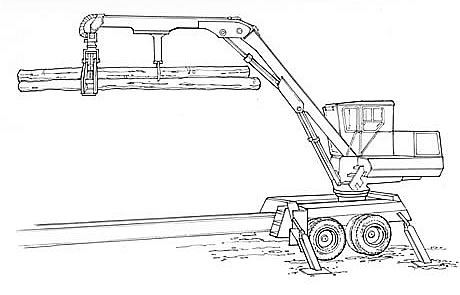
Trailer-mounted knuckleboom loader
Skidders
Skidders are used to drag material from the woods to landings or a roadside. Skidders can be either tracked or wheeled.
Wheeled Skidders
Wheeled skidders are built on articulating chassis with the cab and engine mounted on the front articulation and either a cable drum and arch or grapple mounted on the rear articulation. Wheeled skidders typically have a small blade mounted on the front that is used to push material away and level small obstructions.
Track Skidders
Like wheel skidders, track skidders also use grapples or cables to skid trees. They typically have a full dozer blade on the front end used to create roads and landings. Track skidders come in two styles: rigid track and flex track. Rigid tracked machines consist of a rigid frame supporting the tracks with no suspension. Flex tracked machines have independently suspended bogey wheels supporting the track. As a result of the suspension, flex tracked machines maintain greater contact with the ground and allow for greater traction on broken ground. Tracked skidders are usually used in applications where large loads need to be pulled up steeper slopes, or where a machine that can help build roads and landings is needed.
Skidders are equipped with either a grapple or a cable drum, and sometimes both. Grapples are capable of picking up more than one stem at a time. Grapples are attached to the skidder by an arch or boom, which provides lift and helps position the grapple. There are single arch, double arch, and swing booms.

Wheeled skidder
Forwarders
Forwarders are articulated machines consisting of a cab towing a log bunk. Forwarders can have up to eight wheels and many have a boom mounted grapple used for loading and unloading material. Different sizes of forwarders exist for hauling various log lengths and stem volumes. Forwards differ from skidders by elevating the trees before moving them, thus reducing the impact on the soil.
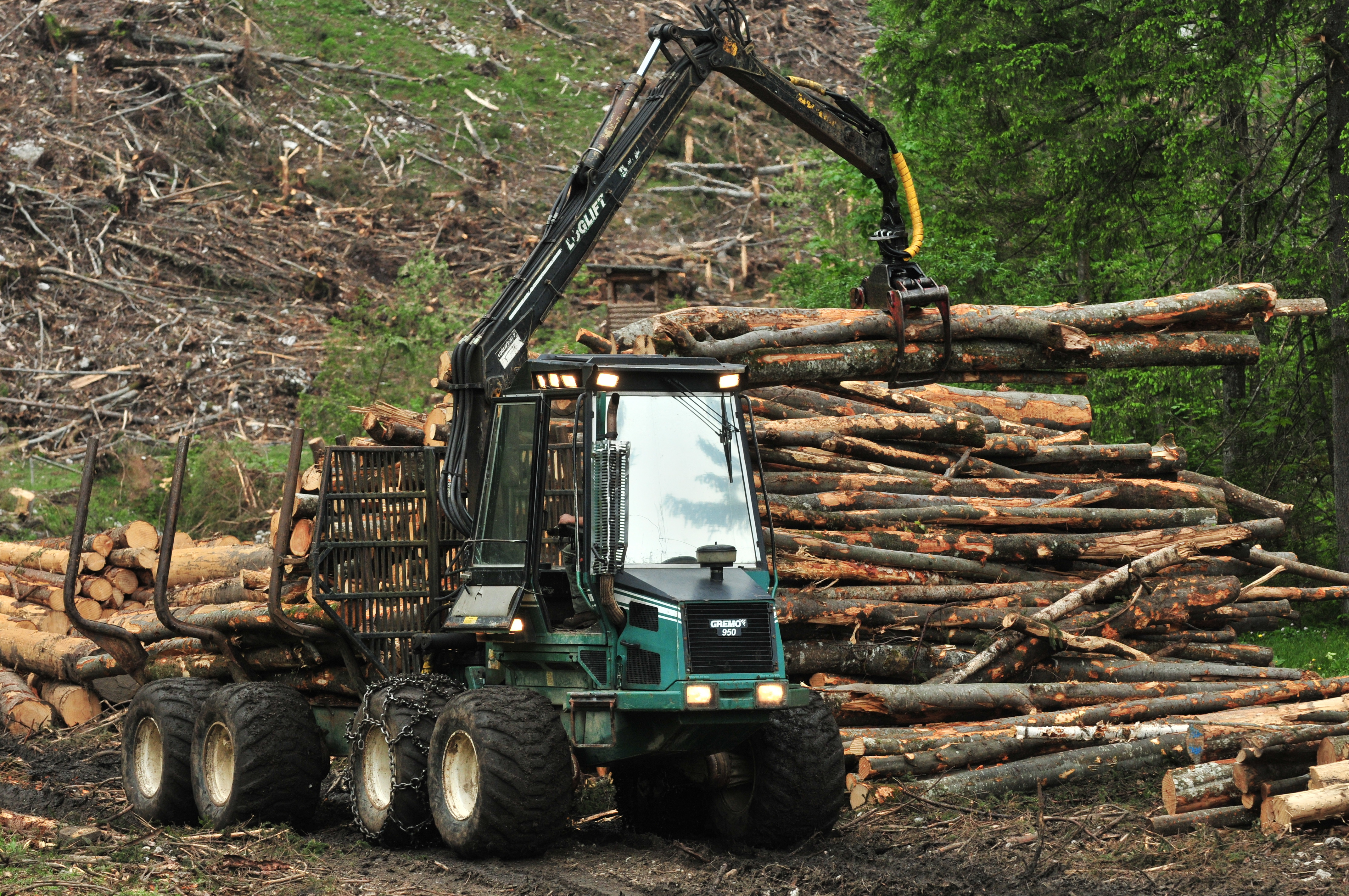
Forwarder loading logs
Mulchers
Mulchers are used to cut, chop, and grind vegetation into small particles that are typically left on-site as mulch. The main purpose of mulching is to lower the volume and vertical height of fuel, for a number of reasons ranging from controlling invasive species to aesthetic treatments. Fuel, in this case, is combustible biomass found in forests. In this case, fuel would be shrubs, branches, downed trees, and logs.
Mulchers can be standalone machines, or attachments mounted on a variety of chassis, such as: skid steers, excavators, farm tractors, wheeled-loaders, and dozers. Mulchers mounted on excavators or wheel loaders are capable of mulching standing trees. Those mounted on skid steers, tractors, and dozers are pushed through trees, and as the stems fall in front of the machine they are shredded. Mulchers come in two types: vertical shaft and horizontal shaft.
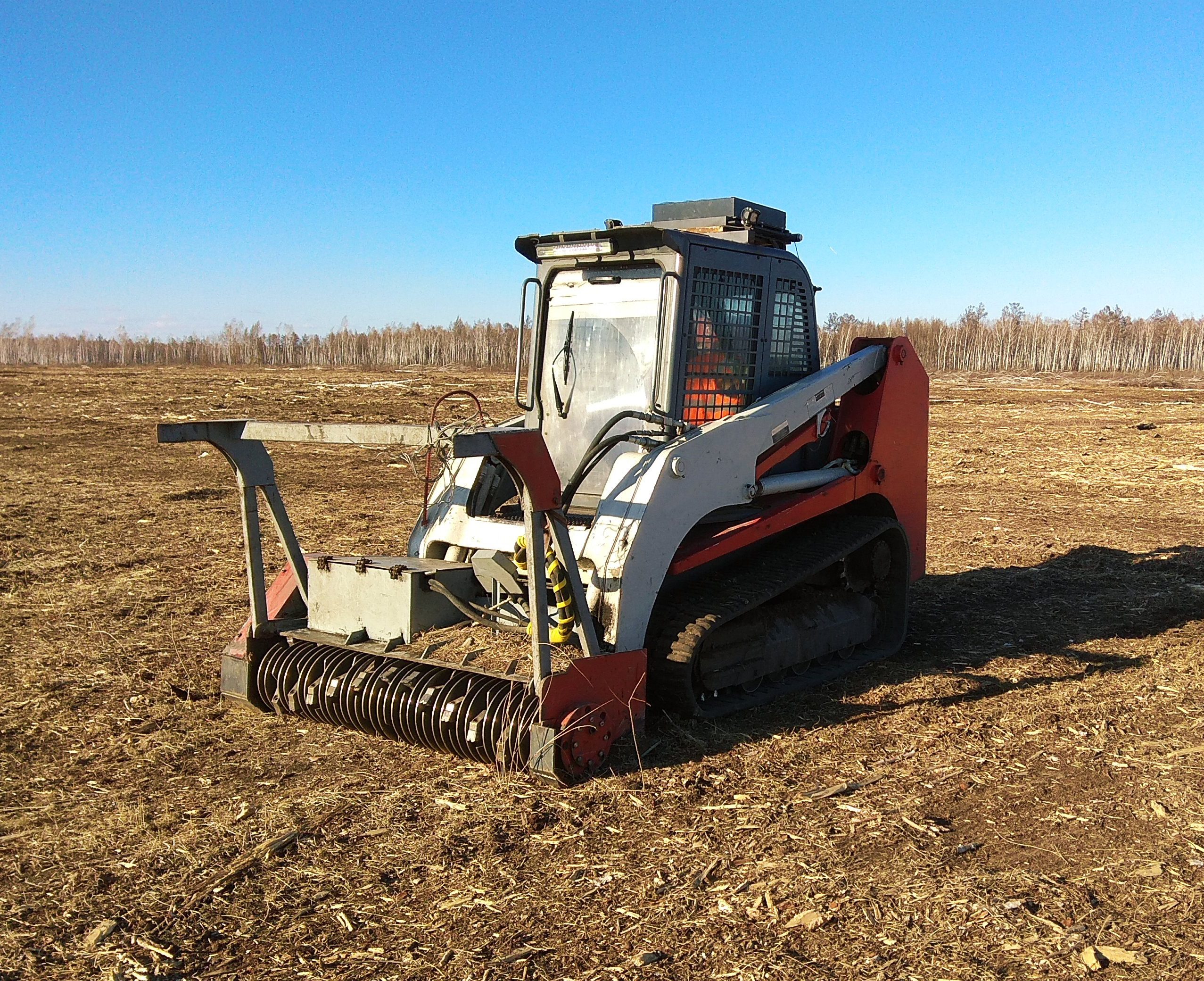
Skid steer with mulcher attachment
Chippers
Chippers are used to reduce trees to uniform sized wood chips. There are many configurations of chippers, but common features of a chipper include: a feeding mechanism, a set of rotating knives (drum or disc mounted), an anvil, and a discharge chute. The chip size is determined by the distance from the anvil to the knives, feed speed, speed of the rotating disc or drum, and distance between the knives. Drum chippers consist of cutting teeth mounted on a rotating cylindrical drum, while disc style chippers have teeth mounted on a large steel disc. Some chippers have integrated delimbing/debarking functions, which is helpful in producing clean chips.
Chippers may be either self-propelled, stand alone, or trailer-mounted. Some chippers have loading arms and grapples for self-loading.

Self-propelled chipper
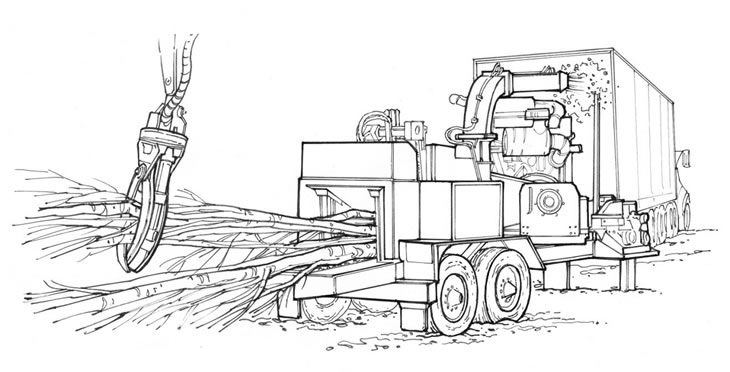
Trailer-mounted chipper
The machines in this post are just some of the most commonly used machines in forestry applications. For additional information on the machines mentioned, as well as others that were not mentioned, check out the U.S. Forest Service’s Forest Operations Equipment Catalog.
Forestry Parts at Iron Wing
At Iron Wing Sales, we carry hard-to-find and No Longer Available parts for all of your forestry needs. Our parts are in-stock and ready to ship now in order to help you minimize downtime. Take a look at our Agriculture & Forestry parts inventory, or search by part #, category, or manufacturer. For further assistance, contact us at: sales@ironwingsales.com or 216-912-9089.